Introduction: Overview of Spot Welding & Seam Welding
Spot welding and seam welding are two of the most commonly used welding processes in the manufacturing industry. Spot welding is a process that uses heat and pressure to join two metal pieces together. It applies an electric current between two electrodes, creating an electrical arc that melts the metal at the point of contact. Seam welding (or arc seam welding), is a similar process, but instead of using two electrodes, it involves running a continuous wire along the seam of two metal pieces to join them together. Spot welding actually a form of seam welding itself! Both are used in automotive and aerospace manufacturing for joining sheet metal components.
What are the Advantages and Disadvantages of Spot Welding & Seam Welding
Spot welding and seam welding are two of the most popular methods for joining metals. Both processes have advantages and disadvantages, depending on the application. Some of the most common benefits and drawbacks are:
Spot welding advantages:
- Low-cost
- Easy to automate
- Portable solutions
Spot welding disadvantages:
- Works best on thin metals only
- Can cause distortion in the material
- Produces weak or small welds if parameters aren’t correct
Seam welding advantages:
- Easily automated
- Produces an air and water tight weld
- Efficient and produces little waste
Seam welding disadvantages:
- Can be relatively slow
- More expensive initial outlay
- Only possible to weld in a straight line
Comparing Spot & Seam Welds from a Cost Perspective
Spot and seam welding are two of the most common techniques used in the industrial sector. Spot welding is an economical solution that involves joining two metal components. It does this by pressing them together and using electric current. Low-cost spot welds can help save costs in certain situations, as spot welding machines are fairly inexpensive and consumable costs are low.
Seam welding is a more expensive process than other welding methods, initial costs for a seam welding machine are more expensive than spot welders, and the process requires a continuous wire to weld the two metal pieces together. Although costs are higher, the results can be sturdier and longer-lasting, making it the only option for some applications.
Which Process is Ideal for What Application?
What are the best uses for spot vs. seam welding? Spot welding is ideal for joining thin sheets of metal. Making it ideal for light duty applications including electronics and battery manufacturing. It is also widely used in the automotive sector, due to it’s ease of automation in high-volume production lines.
While seam welding is best suited for joining thicker materials, or creating a continuous weld along a seam. Thus making it ideal for the fabrication of tanks and vessels, as well other pipe and tube welding applications.
Conclusion: Choosing between Spot Welder & Seam Welder for Your Project Needs
When it comes to welding, choosing the right process for your project needs is essential. Consider the end use of the component, does the weld need to be air or water tight? What is the material and thickness to be welded? Also what is the budget for the project.
When you take into account these tips, it should be easier to decide which process is right for your welding project. Need a machine? Take a look at our current stock of new and used spot welders and seam welders.
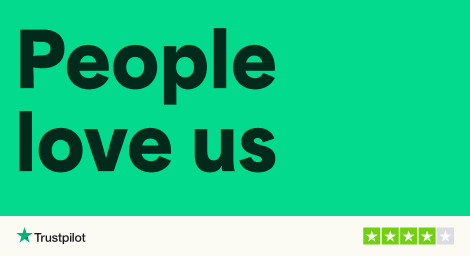
comments
Pingback: Comparing Spot and Seam Welding: What’s the Difference? – Dubegarages.com