In many industries, crucial parts are exposed to harsh, demanding conditions. Metal fabricators need a way to prolong the life of these parts, avoiding costly repairs and damage. That can often lead to catastrophic results in industries like construction, and oil and gas.
*Updated January 2025*
Key Takeaways:
- The weld overlay and cladding process provides critical protection for vulnerable fittings.
- Welding overlay is a process that applies one or more additional metals to the base metal using fusion welding. These materials are mainly chosen for their corrosion resistance and are applied to improve the base material’s properties.
- Weld cladding can use either fusion welding or other mechanical forms like hot rolling to apply an additional material layer. This metal should have high-strength properties to improve this in the base material.
- Industries that benefit from these critical processes include heavy industry, mining, oil and gas, and renewable energy.
- The equipment consists of a mechanised welding torch, mounted onto a carriageway to apply the metal overlay. Workpieces are handled precisely by a welding manipulator like a positioner to ensure accurate results.
Table of Contents
- The difference between overlay welding and clad welding.
- What is welding overlay?
- What is weld cladding?
- Applications and industries that utilise these processes.
- Equipment needed to perform weld cladding and overlay.
- New technology for weld cladding and overlay machines.
What is the Difference Between Weld Overlay and Cladding?
Both weld cladding and overlay form a heavy-duty, metallurgically-bonded protective layer that will not be undermined or dislodged in service. They are critical processes in many industry sectors, where service conditions require corrosion-resistant properties. Although similar, there are subtle differences in each process.
In overlay welding, one or more metals of similar properties are fusion welded to the base layer. These additional materials are chosen for their corrosion resistance, improving this function in the base material.
Cladding welding, however, is applied to increase the strength of the base metal, reflected in the high-strength materials used in this process. While weld overlay uses materials similar to the base metal, weld cladding is also suitable for dissimilar metals. As well as fusion welding, weld cladding can also be applied using other mechanical methods like hot rolling.
What is the Weld Overlay Process?
The highly versatile weld overlay process provides the practical combination of readily available base materials, coated with a suitable corrosion-resistant alloy to protect any given area.
Fusion welding methods used for overlay welding include MIG (metal inert gas), TIG (tungsten inert gas), SMAW (shielded metal arc welding), and other forms of arc welding like SAW (submerged arc welding).
One of the main benefits of this process is the cost savings. It enables you to use an inexpensive metal, such as carbon steel, for fabrication, applying a more expensive but corrosion-resistant layer of stainless steel afterwards.
Typical welding alloy materials include Inconel 625, Inconel 825, Monel, Hastelloy, stainless steel, nickel and chromium.
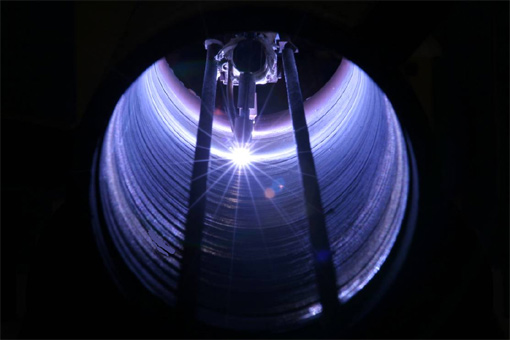
What is Weld Cladding?
Used to improve the strength of a metal component, welding cladding is the process of applying a high-strength alloy layer to a base metal.
Like weld overlay, the process can be applied using fusion welding, or other mechanical methods like hot rolling or powder metallurgy. You can also use dissimilar materials, unlike those used in overlay welding.
Clad welding offers material and weight savings when a high-strength, quenched and tempered steel is used in a corrosive environment. Improving the strength of the component, weld cladding helps protect against general operational damage like friction, abrasion, and heat stress.
Weld Cladding Overlay Applications and Industries.
A wide range of applications can benefit from these forms of metal overlay.
The anti-corrosion advantages of overlay welding make it perfect for use in industries like subsea, petrochemical, and oil and gas.
Applied to components including pipes, flanges, and valves, welding overlay not only reduces manufacturing costs but also helps to prolong the life of these critical parts.
Offering the same advantages, clad welding is used where material strength is paramount. Applications like manufacturing boiler tubes and pipes and industrial pipelines benefit from its strengthening ability. Plus specialist fabrications for hostile environments like engine rooms and mines also take advantage of its capability to protect against abrasive damage.
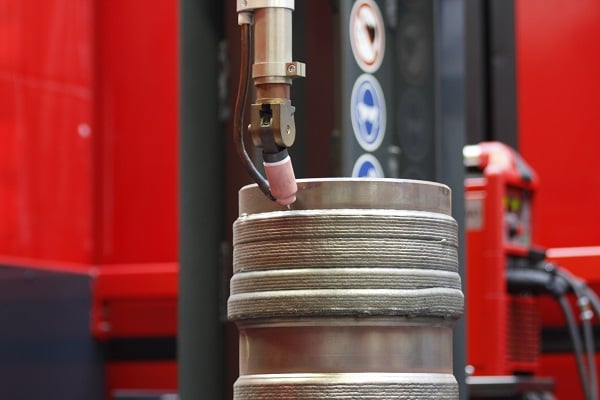
Equipment Used in Clad Welding and Overlay
Overlay welding machines and clad welders are built of multiple components to form the final system.
For overlay welding, these can be bespoke depending on the job requirement, but will all feature:
- A welding manipulator, designed to handle the weldment during the overlay process.
- A Control unit to apply the desired program according to the job inputted by the operator.
- A Carriageway or similar, such as a column and boom or beam welding system, to facilitate the travel of the welding head.
- A welding torch that applies the weld overlay.
- A welding power source, such as a hot wire tig, or MIG welding machine, depending on the requirements of the project.
In weld cladding operations, the component is mounted on a turntable, with the bore to be welded centred on the turntable rotational axis. During the cladding operation, the turntable rotates and the welding torch is stationary (moving up once a revolution). A conventional column & boom (rack & pinion type) supports precision cross slides attached to the end of the boom. The slides perform the task of moving the torch in two or more axes.
A typical weld cladding system consists of:
- A rack & pinion drive type column & boom for approximate 1. positioning of the welding torch.
- A cross-slide assembly for precise control of the torch.
- System control unit.
- Arc Control Unit for arc initiation, voltage and current detection.
- Welding Power Source: usually around 350Amp, 100% duty cycle
- Hotwire Power Supply, such as the PEC HWT-75 (75Amp, 100% duty cycle).
- Water cooler for cooling the welding torch.
- Welding torches (for example Fronius HVATT, HST, SBT) in lengths from 750 – 1750mm.
- Turntables and welding positioners, typically up to 10,000kg capacity.
- Operator pendant controls.
New Technologies: Rotary Welding Heads and Hot Wire Welding.
For as long as arc welding has been around, the welder would either manually move his welding torch around the joint or surface he is welding, or mount it on a turntable for mechanised rotation of the part. Oil & Gas industry wellhead valves have become heavier (50 tons) and have more complex shaped bores that require the component to be mounted ‘off centre’ to the table rotating axis. This results in accelerated wear of the supporting bearings and drive gears of the turntable. Centring a bore on a large block valve to the table centre is also time-consuming and a strenuous task for the operator.
Faced with these ongoing issues with conventional cladding technology, a breakthrough was made in weld cladding technology by replacing the turntable altogether and rotating the torch instead of the component (which remains stationary). The torch is mounted on a weld head that rotates which gives rise to the name ‘Rotary Head’.
A new technology in the welding process for weld overlay and cladding is hot wire welding. Although invented many years ago, this technology never saw the light of day until recently. Hotwire welding and cladding was the subject of a one-day conference at the FabTech Int’l and AWS Welding Show in Chicago, with presentations on hot wire GTAW and hot wire plasma processes.
Featuring the popular use of hot wire tig cladding of tube and piping for the offshore oil and gas industries. Plus hot wire GTA “narrow groove” welding and its superior performance on titanium. Advantages are increased deposition rates and faster travel speeds.
The hot wire tig process has increased in popularity over multiple groove welding, build-up and cladding operations. Commercially available and specialised hot wire equipment continues to promote the usage of the process for producing high-quality welds. Industries including nuclear, power generation, pressure vessels and offshore oil are common areas of application.
Where a considerable amount of work is directed toward pressure vessel fabrication, hot wire gas tungsten arc welding is used extensively for the narrow gap welding of nickel-based alloys. As well as build-ups, butterings, and cladding of high-strength low-alloy steel.
If you’re an engineering company that undertakes overlay welding or weld cladding, have you thought about buying used equipment? Having supplied and purchased a range of Fronius, Welding Alloys, and TPS machines Worldwide, our client base includes the likes of Wellbore Integrity Solutions, SRI Energy, and OneSubsea. Whether you’re looking to invest in another overlay welding machine, or have a system surplus to requirements, get in touch to find out more.
comments
Good article, thanks for sharing. However, is there any difference between overlay weld and surfacing?
Hi, I think it’s just a different term for an overlay weld. Depends where in the World you are too!
Thanks for writing on the cladding process, I’m not familiar with this word because I’m a learner, and learning welding as of now. But I will like to tell here that I found this term first time.
great