Introduction: What is Plasma Cutting and How Does it Work?
Plasma cutting is a process of cutting and shaping conductive materials. It is a key process in industrial and metal fabrication. Plasma cutting works by forcing a gas, typically compressed air, through a small channel or nozzle. An electrical arc is then used to ionize the gas, forming plasma which is a high-temperature and ionized gas. This plasma is then forced through the nozzle at high speed towards the metal workpiece.
As the plasma flow comes into contact with the metal, it heats the metal up to its melting point. The molten material is then blown away with the high-velocity plasma stream. The process is repeated along the cutting path, creating a narrow kerf with the molten metal blown out of the cut. CNC plasma cutting machines use computer-controlled movement to direct the path of the plasma stream. This allows for accurate and intricate cuts.
Plasma cutting is suitable for a variety of electrically conductive materials. These include stainless steel, aluminum, copper alloys, and mild steel. Plasma can cut through material thicknesses ranging from thin gauge sheets up to several inches thick. It is an efficient and cost-effective method for metal fabrication processes needing precise and complex cutting.
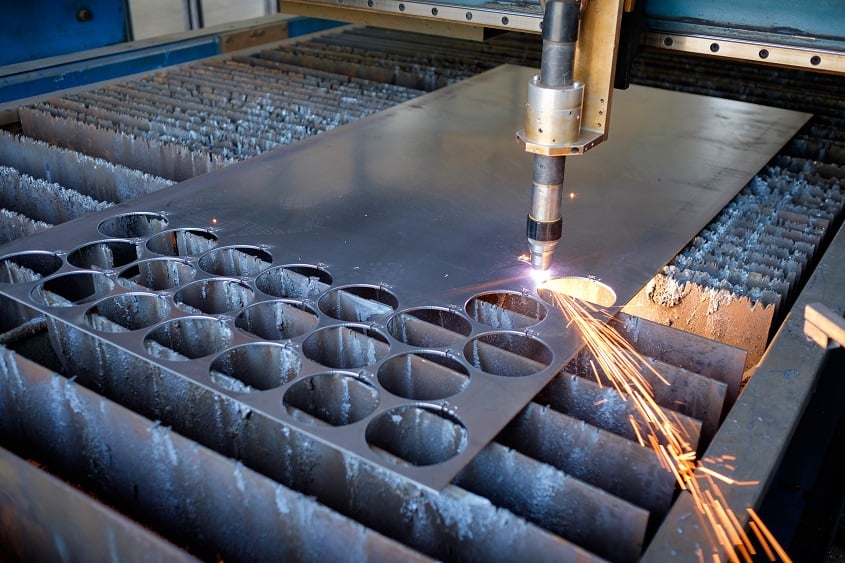
The Benefits of Using Plasma Cutters for Stainless Steel
Plasma cutting is a popular method for cutting stainless steel due to the many benefits that it provides. Some benefits of using plasma cutters for stainless steel include:
- High precision: Plasma cutters are accurate and produce clean, precise cuts. This is especially important when working with stainless steel. Which often requires very precise cuts to ensure a quality finished product.
- Fast cutting speed: Plasma cutters can cut through stainless steel at a very high speed. This can reduce production time and increase throughput for metal fabrication processes.
- Versatility: Plasma cutters can cut through a wide range of stainless steel thicknesses. This makes them ideal for a variety of applications and industries. Including automotive, aerospace, and construction.
- Cleaner cuts: Plasma cutting produces a narrow kerf and a small heat-affected zone (HAZ). This reduces the amount of warping and distortion that can occur during the cutting process. Thus resulting in cleaner, more accurate cuts, and a better-quality finished product.
- Cost effective: Plasma cutting is a cost-effective method for cutting stainless steel. Especially when compared to other cutting methods such as laser cutting. The equipment required for plasma cutting is less, and maintenance costs are low.
Tips & Techniques on Choosing the Right Plasma Cutter for Stainless Steel
When it comes to choosing the right plasma cutter for stainless steel, there are several things to consider. These include checking the recommended cut capacity for the machine. This is especially important if you are working with thicker stainless steel. When cutting stainless steel, precision is key. Look for a machine with high-precision technology. This includes features like CNC controls, automatic torch height control, and clean cut technology. The power output of a plasma cutter is one of the most important factors to consider. Look for a machine with at least 40 amps of output to cut through stainless steel. Check the cutting speed, this is a vital factor when it comes to choosing the right plasma cutter for stainless steel. Look for a machine that can cut at a high speed to prevent the material from warping or distorting. Check the gas type. When it comes to stainless steel, nitrogen gas is the most common because it doesn’t react with the material. Check the gas requirements for the machine and make sure it can handle nitrogen gas.
Troubleshooting Tips for Plasma Cutting Stainless Steel
Experiencing issues with plasma cutting stainless steel? Here are some troubleshooting tips to help you overcome the problem:
- Excessive dross. Dross is the molten metal that appears on the surface of the material after cutting. If you’re experiencing excessive dross, check your plasma gas flow and make sure it’s set to the recommended rate. You can also try using a nitrogen plasma gas for cleaner cuts.
- Warped or distorted material. If your material is warping or distorting during the cutting process, you may be cutting too slowly. It might also be possible you’re using too much power. Try adjusting the speed and power levels to see if that helps.
- Poor cut quality. Poor cut quality can occur if your machine is not maintained. The plasma cutting consumables could also need replacing. Check your machine’s consumables, including the nozzle, electrode, and shield. Replace where necessary.
- Arc instability. An unstable arc can cause issues with the cut quality and increase dross. Check your machine’s ground connection and make sure it’s grounded. You can also try adjusting the gas flow rate and machine settings to stabilize the arc.
- Uneven cuts. Uneven cuts can down to a variety of factors. The main culprits include material thickness, power settings, and gas pressure. Check your machine settings and make sure they’re appropriate for the material.. You can also try adjusting your torch height and angle to ensure a consistent cut.
- Torch consumables wear out quickly. Torch consumables wearing out too fast? It could be a sign that you’re using too high of a power setting or cut speeds are too slow. Check your machine settings and try adjusting them to extend the life of your consumables.
What Are the Safety Precautions to Consider When Working With a Plasma Cutter?
Plasma cutting is a powerful and effective cutting method requiring high temperatures and electrical currents. As such, there are various safety considerations that you should take into account when working with a plasma cutter. These include:
Electrical Safety
The first safety consideration when working with a plasma cutter is electrical safety. Plasma cutting involves using high voltage currents to produce the plasma that cuts the metal. So avoid touching the nozzle of the plasma cutter or the workpiece during operation. Also, ensure that your plasma cutter has a ground wire and that it is grounded before use.
Protective Clothing and Gear
When working with a plasma cutter, it is essential to wear protective clothing and gear. Plasma cutting produces very high temperatures that can burn unprotected skin. As such, wear leather gloves, welding jackets, and pants to protect your skin. Additionally, wear safety glasses or a welding helmet to protect your eyes from sparks and light produced.
Ventilation
Plasma cutting produces a lot of fumes and gases that can be dangerous to inhale. Proper ventilation is essential to ensure that you do not inhale these fumes. Ensure that your workspace is well-ventilated before beginning work. If you are working in a small space, consider using a fume extractor. Or try wearing a respirator to protect yourself from inhaling toxic fumes.
Fire Safety
Plasma cutting produces sparks that can ignite flammable materials. As such, ensure that your workspace is free of any potential fire hazards. Avoid working in areas that contain flammable liquids, gases, or materials. Additionally, have a fire extinguisher nearby in case of a fire.
Equipment Maintenace
Finally, you’ll need to maintain your plasma cutter equipment. Regular maintenance ensures that your plasma cutter is working properly and safely. Inspect your equipment before use to ensure that everything is working. Replacing any worn or damaged parts as necessary.
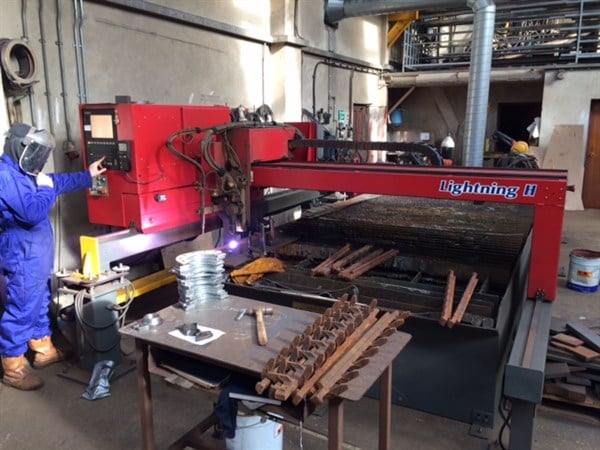
How to Maintain Your CNC Plasma Cutting Machine After Use.
Maintaining a CNC plasma cutter is essential to ensure that the machine continues to function correctly. Producing accurate cuts, and lasting for its expected lifespan. Below are some tips on how to maintain a CNC plasma cutter:
Keep the Machine Clean.
Keeping the plasma cutter clean is one of the most critical aspects of machine maintenance. Check the equipment and remove any dirt, dust or debris that may have accumulated in or around the machine. These particles can lead to malfunctions, so cleaning is important. Clean the nozzles, the cutting bed, and the air filters regularly.
Check the Consumables.
The consumables of the plasma cutter are the parts that wear out over time when used. These include the electrode, the nozzle, and the shield cup. Inspect these parts and check for any signs of wear or tear, and replace them if necessary. Checking the condition of the consumables ensures that they are in good working order.
Lubricate the Machine.
Lubrication is necessary for the smooth operation of the CNC plasma cutter. Check the manual for recommended lubricants and follow the instructions to lubricate the moving parts of the machine. These might include items such as the rails, ball bearings, and lead screws.
Conduct Regular Maintenance.
To ensure that the machine continues to function properly, conduct regular maintenance activities. Follow the maintenance schedule provided in the machine manual. Which includes tasks such as cleaning, inspecting consumables, and conducting necessary repairs.
Calibrate the Machine.
Calibration of the CNC plasma cutter is vital to make sure that the machine produces accurate cuts. Regular calibrations ensure that measurements are exact and keeps the cut finish precise.
Keep Software Up-To-Date.
Like any other electronic product, it’s vital to keep the software running on the CNC plasma cutter up-to-date. Check for updates, and install any necessary software patches. This will help to prevent machine malfunctions caused by outdated software.
comments
Pingback: What You Need to Know About Plasma Cutting Stainless Steel – Ride-gear-up.com
Pingback: What You Need to Know About Plasma Cutting Stainless Steel – Mechanicfeed.com
Pingback: What You Need to Know About Plasma Cutting Stainless Steel - Autotruckpartsoutlet.com
Pingback: What You Need to Know About Plasma Cutting Stainless Steel – Tracktodirt.com
Pingback: What You Need to Know About Plasma Cutting Stainless Steel – Mynewcaraccessories.com