Pulse MIG welding is a modified spray transfer MIG process that allows exceptional heat input control, better operating characteristics, and higher weld quality than standard MIG.
Are you experiencing distortion, burn-through, or negative material property changes when welding exotic metals like aluminium, stainless steel, and high-strength steel? The vast majority of these issues stem from excessive heat input. The solution? — Pulsed welding processes, like pulsed MIG or TIG.
However, pulsed MIG does so much more than preventing heat-related issues. Read on to discover how pulse MIG welding works, its applications, and how your business can benefit from its advantages over conventional MIG welding.
What Is Pulse MIG Welding and How It Works
Pulse MIG is a modification of the spray transfer MIG welding process. By alternating between the high (peak) and low (background) current, pulse MIG reduces the average heat input into the metal. In addition, pulse MIG times the peak current just right for maximum efficiency and deposition rate.
The pulsed MIG arc alternates between the two phases:
- The hot phase, where the molten drop of filler wire is deposited into the joint.
- The “cooler” phase, which keeps the arc going but doesn’t deposit the filler metal.
The second phase lets the puddle cool slightly, which prevents burn-through, distortion, and many negative material property changes.
Double Pulse MIG Welding
Double-pulsed MIG welding, sometimes called dual-pulse or pulse-on-pulse, adds a second pulse to the standard pulsed MIG mode. The first pulse acts as a regular pulsed MIG, while the second pulse significantly reduces the current output, additionally decreasing the heat input and timing the weld puddle cooling action. As a result, you get the benefit of standard pulsed MIG, but the second pulse cools the puddle to achieve a TIG-like “stack-of-dimes” weld appearance.
The first pulse (with its own high and low current) deposits the metal during its peak current. Since the first pulse has a background current phase, you get all the benefits of a single pulse. However, the second pulse turns the first pulse off without extinguishing the arc. This is achieved by a significant current output reduction while keeping the arc on. So, when the first pulse finishes its metal deposition, the second pulse lets the weld cool before the first pulse continues depositing metal, resulting in a stack-of-dimes appearance.
Pulse MIG Welding vs. Conventional MIG Transfer Modes
Most MIG welding applications use a short-circuit transfer mode. But, almost all MIG power sources can be configured to run globular and spray transfer modes as well. However, pulsed MIG requires a power source designed for pulsing the spray transfer output. So, standard MIG machines cannot provide the benefit of pulsed MIG power sources.
Pulsed MIG welding is better in almost every way than conventional MIG transfer modes. While each transfer mode has pros and cons, pulse welders amplify their advantages and eliminate most negatives.
Short circuit MIG works by feeding the wire into the weld joint, where it physically touches the grounded metal (work clamp attached to it) and closes the circuit. Due to electrical flow resistance, the wire melts and deposits into the joint at the point of contact. Short circuit transfer works well for thinner metals. But its disadvantages are a low deposition rate and high spatter. Since the wire practically explodes at the point of contact, a lot of spatter is produced.
Globular MIG transfer is rarely used due to extreme spatter. It works similarly to short circuit but with more filler wire. A lot of filler metal is lost to spatter, making globular transfer inefficient.
Spray MIG transfer sprays the molten filler wire as a stream of tiny metal droplets. Since the wire never physically touches the joint, it never shorts and doesn’t cause spatter. Spray arc transfer offers exceptional deposition rates, deep weld fusion, and works great for thick metals. But, the weld puddle becomes too liquid with spray transfer, making out-of-position welding difficult. In addition, spray transfer is too hot for thin metals, which can lead to burn-through and excessive distortion.
Pulsed MIG is a modified spray arc transfer mode where the current drops and rises at a high frequency. Basically, pulsed MIG offers the same benefits as standard spray transfer. But, it doesn’t run as hot and the puddle is not as liquid, making it easy to weld in all positions and join thin and thick metals alike.
Pulse MIG Welding vs. TIG Welding
The TIG welding process produces the highest welding quality and aesthetic appearance of all arc welding processes. But, it’s challenging to master and has a low deposition rate and travel speed.
Pulsed MIG offers similar weld quality, but with a significantly higher deposition rate and travel speed. In addition, double-pulsed MIG can mimic the TIG-like weld appearance, making it an excellent choice where visual weld quality is paramount.
Benefits of Pulse MIG Welding
Many businesses have improved their productivity and bottom line thanks to pulsed MIG advantages. This welding process is especially beneficial when welding sensitive materials like stainless steel and aluminium.
Heat Input Reduction
Not only does pulsed MIG prevent warping and burn-through on thin materials, but it can help you avoid losing favorable metal characteristics by controlling heat input.
For example, stainless steel can lose corrosion resistance if the heat affected zone (HAZ) is overheated. If austenitic stainless steels are held at critical temperatures (427 to 871°C) for too long, chromium carbides can precipitate. As a result, the chromium content can deplete at grain boundaries, leading to intergranural corrosion. Pulsed MIG is an excellent welding process to avoid excessive heat input and to keep the stainless steel corrosion-resistant post-welding.
The heat reduction of pulsed MIG is also beneficial for welding nickel alloys, aluminium, high-strength steels (HSS), and ultra-high-strength steels (UHSS).
Significantly Less Spatter
Pulsed MIG can improve your productivity by reducing the amount of post-welding work, like spatter removal. Short-circuit MIG creates a lot of spatter that often needs to be chipped off or ground off with an angle grinder. This non-value-adding activity reduces the operator’s efficiency. So, pulsed MIG saves time and improves shop productivity by eliminating spatter in welding.
Reduced Welding Fumes Production
Since the pulsed MIG reduces the average energy output, less welding wire is vaporized. As a result, the production of welding fumes is reduced. While pulsed MIG cannot be used on its own as an effective fume engineering control, it helps lessen the effects of welding fumes.
Wire Savings with Pulse MIG Welding
Pulsed MIG welding cuts the costs of filler metal wires in three ways:
- Less spatter means more wire is deposited into the joint instead of ending up as a spatter that must be removed from the welded metal surface.
- You can have a wider operating range of a wire when using pulsed MIG machines. So, instead of stocking multiple wire diameters, you can stock just one or two wires for various applications. Buying a large spool of one-diameter wire is less costly than buying multiple smaller spools of different diameters.
- Saving time on wire changeovers improves your productivity and bottom line.
Improved Weld Aesthetics
Standard pulsed MIG makes better-looking welds than short-circuit MIG, flux-cored, or stick welding processes. In addition, double-pulsed MIG can produce welds similar to TIG in appearance, making it an excellent choice for applications where perfect weld looks are crucial.
Works In All Positions
Unlike regular spray transfer, you can use pulsed MIG to weld in all positions. Thanks to its low current phase, the puddle cools slightly and gains the necessary rigidness not to fall down due to gravity.
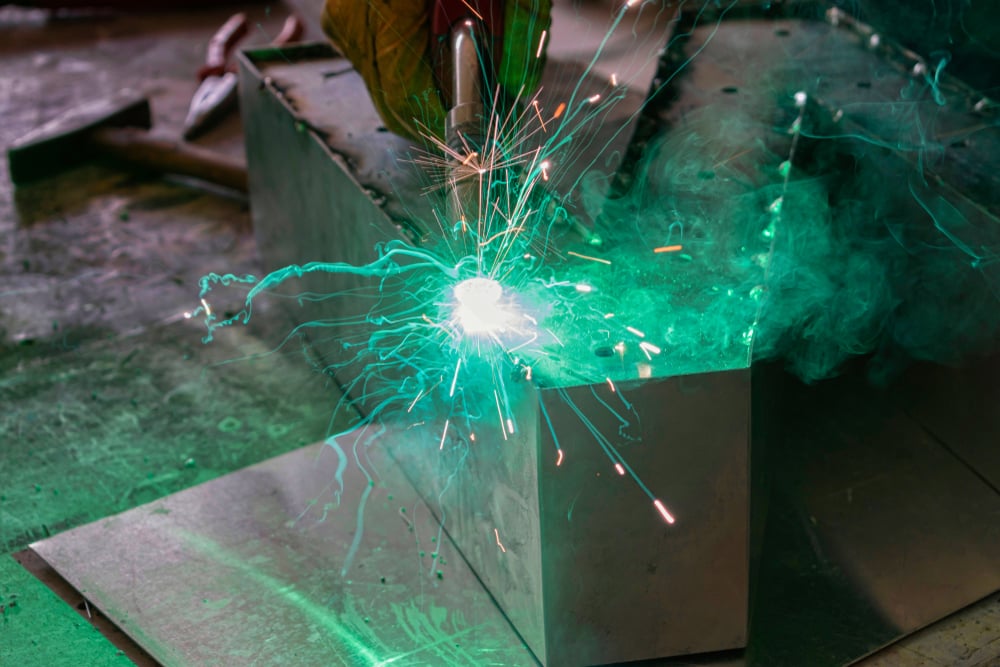
Pulse MIG Welding Applications
Aluminium Pulse MIG Welding
Aluminium welding is the primary pulsed MIG application because it allows high deposition rates without the fear of burn-through. Typically, aluminium MIG welding is performed in the standard spray transfer mode because short circuit is too cold for aluminium.
Since aluminium is an excellent heat conductor, it needs a high heat input. But, aluminium also has a low melting point. So, it’s challenging to find the sweet spot to avoid burning through, especially when welding thin aluminium. So, using pulsed MIG gives you the best of both worlds. The peak current melts the aluminium, while the background current prevents burn-though and warping.
Welding Sensitive Alloys
Pulsed MIG is often used in auto body collision repair. Some car manufacturers mandate pulsed MIG welding to prevent heat from negatively affecting the car body parts. The automotive industry uses aluminium and highly specialized advanced high-strength (AHSS) and ultra-high-strength steels (UHSS) to lighten the vehicles and meet emissions regulations. But, these materials are sensitive to heat. Excessive heat input can drastically increase hardness, cause distortion, and significantly increase the probability of cracking.
Stainless steel and nickel-based alloys are also sensitive to heat input and benefit from pulsed MIG. This is especially true on thin sections and visible welds where weld appearance is essential.
Filling Holes and Large Grooves
Thanks to highly efficient wire use and high deposition rates, pulsed MIG allows you to quickly fill large grooves. And low heat input prevents the weld root from burning through.
Out Of Position Welding
HVAC, pipe welding, construction jobs, or other applications where a welding operator finds themselves under the weld puddle benefits from pulsed MIG. Since the background current lets the puddle cool slightly, it gains rigidity and resists the gravitational pull.
Which Pulse MIG Welders Are The Best
Pulse MIG welders are challenging to manufacture because the internal circuitry must meet many demands to produce a good MIG weld. Since pulse output quality depends on the programming to adapt to different welding wires, material types, and shielding gasses, it’s paramount to choose a welder from a reputable brand. Some of the best pulsed MIG welding brands are Fronius, Lincoln Electric, Miller, ESAB, and GYS. In addition, synergic MIG welding pulse machines are the best choice for ease of use. Synergic MIG auto-sets most settings for you, making pulsed MIG accessible and quick to implement.
Besides the power source, it’s vital to choose a high-quality wire feeder for stable pulsed MIG. Since this process is highly reliant on wire feeding accuracy, any slippage may negatively impact the end result.
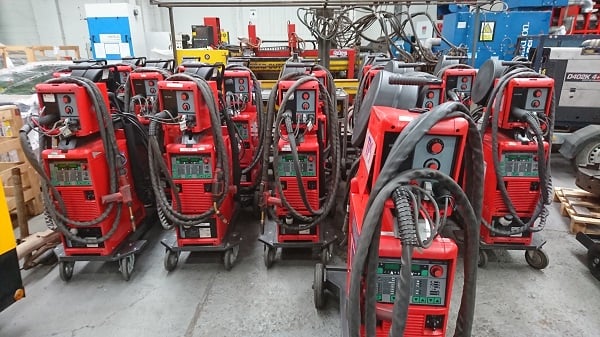
Westermans – Your Partner In The Ever Evolving Welding Industry
If you are looking to buy or sell a pulsed MIG welding system, Westermans is here for you. We stay on top of the changes in the welding industry and are always ready to support your equipment needs. Contact us today, and our expert team will help you choose a suitable pulsed MIG welder or other equipment you may need.
comments
Pingback: Pulse Welding For New Welders: Precision, Speed, and Efficiency