No other welding technology can match the quality of orbital for tube and pipe welding. So, let’s dive into orbital welding applications. Learn how it benefits almost every major industry in the World!
Updated 07/04/2025
Key Takeaways:
- Orbital welding plays a key role in some of the World’s most critical industries
- Some of our most commonly used technologies wouldn’t exist without orbital welding
- Orbital welding is an automated process for clean, repetitive welds of pipe and tube
- Industries include food and beverage, semi-conductor, oil and gas, and pharmaceutical
Contents:
- Introduction
- About the orbital welding process
- Orbital welding applications
- Food, dairy & beverage
- Semiconductor industry
- Oil & gas
- Pharmaceutical & biotechnology
- Aerospace
- Power Generation
- Shipbuilding
Introduction to Orbital Welding Applications:
Automated orbital welding systems are among the core technologies that enable the modern world to function. The preciseness, consistency, and productivity of orbital welding benefits many industries. From pharmaceutical to aerospace, orbital welding applications play a huge role.
We couldn’t have modern planes or smartphones, as chip manufacturing uses orbital welding. So, the device you are using to read our blog would be more challenging to make without orbital welding. Providing the necessary weld integrity for semiconductor stainless steel processing lines. Oh, and the price of oil and gas would probably be higher without the use of orbital welding.
What Is Orbital Welding?
Orbital welding is an automated method where the torch rotates around a static tube or pipe. The 360-degree rotation provides a consistent weld speed, tip-to-joint distance, and weld quality.
Orbital welding removes human error, as well as providing repeatable weld results. Benefits include greater efficiency, safety, and joint quality. You can use many arc welding processes with this automation method. We will be focussing on TIG welding in this article, as it’s the most common. You can learn more about how orbital welding works in our separate guide.
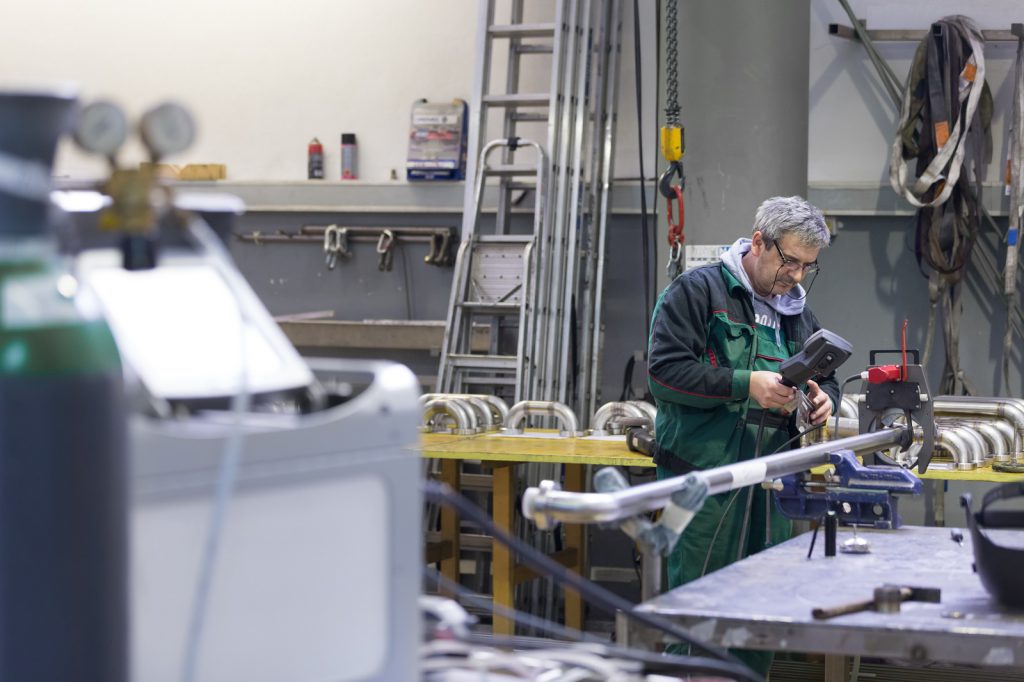
Orbital Welding Applications.
TIG orbital welding provides the cleanest welds. This is thanks to it’s focused arc and non-consumable tungsten electrode. Most critical orbital welding applications rely on TIG welding. This is because it allows perfect accuracy and exceptional heat input control. As well as it’s main draw; virtually contamination-free welds. So, if you are unsure when to use orbital welding, the answer is whenever you need to join tubes and pipes for costly equipment and critical lines.
Thanks to TIG versatility, orbital welding applications include almost all metals. You can join aluminium, magnesium, titanium, stainless steel, and exotic alloys. Achieving near-perfect welds on each!
Food, Dairy, And Beverage.
The food, dairy, and beverage industries are heavily regulated to improve food safety and quality. Which includes the welds joining the pipes, tubes, fittings, and equipment. The sanitary pipe welds must have consistent, full penetration. With their surface needing to be smooth and without crevices. This prevents bacterial growth and meet the strict sanitary stainless welding requirements.
The majority of food, dairy, and beverage production requires stainless steel tube welding. This material is resistant to corrosion and contamination. But, it’s also prone to carbon precipitation if overheated during the welding process. This could lead to the loss of corrosion resistance.
The precision of computer-controlled orbital welders ensures consistency. As well as accurate tungsten rotation around the pipe/tube. Preventing excessive heat input and ensuring the continuation of corrosion resistance.
Semiconductor Industry.
Semiconductor production relies on miles of stainless steel processing lines. These transport toxic and corrosive gasses necessary for chip production. These tubes must not distort from heat input or lose corrosion resistance. Plus, the greatest weld purity and integrity are non-negotiable.
The orbital TIG welding process has been the industry’s standard since the early 1980s. Today, it’s the most reliable way to meet the needed weld quality and flexibility. As well as the ever-increasing stringent requirements of the semiconductor industry. Usually, an enclosed weld head provides the greatest weld shielding and cutting oxidation of the bead. Contractors in the semiconductor industry often use Magnatech, Orbitalum, and AMI orbital welders. This is due to their high-quality software, precision, and reliability.
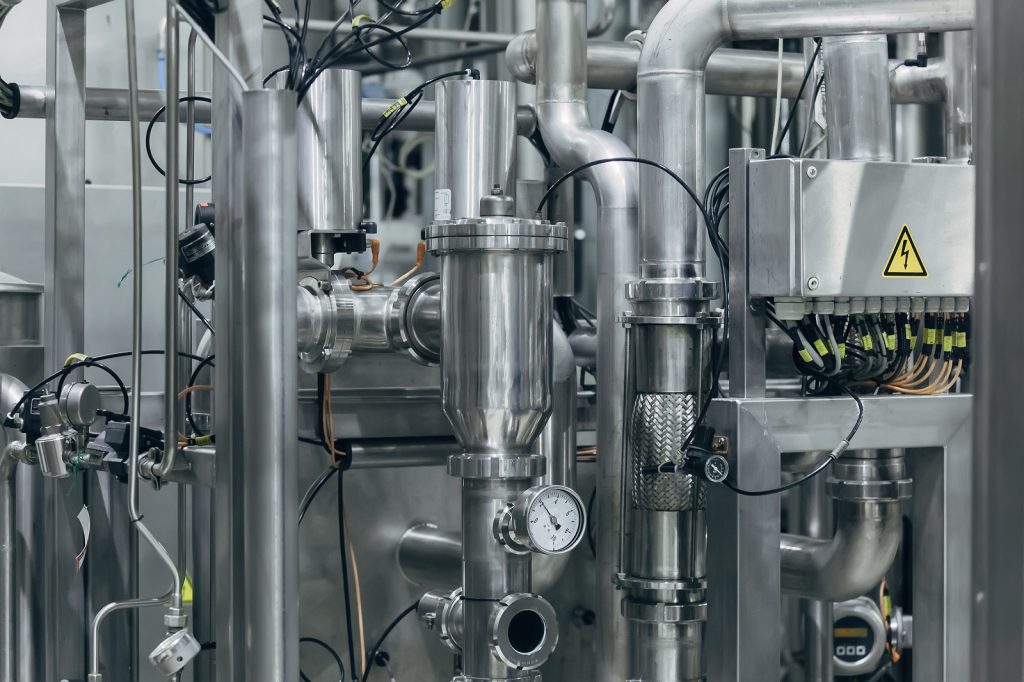
Oil and Gas Pipe Welding.
In offshore drilling or transportation of crude oil, some contractors still use manual welding methods. These include stick/MMA, MIG, or manual GTAW. However automated orbital welding offers higher productivity and safety.
Everything from the tubular construction of oil platforms, to stainless steel pipes on the sea floor. Many applications in this industry benefit from orbital TIG welding. Take offshore rigs, crude transport pipelines, and tubes and pipes in petrochemical plants. They all must be welded with absolute integrity. A single weld inspection failure prolongs the time to pipeline completion. Thus creating a bottleneck, since you can only lay pipes one after another. But, it’s even worse when the welds fail in service due to the corrosive chemicals they carry. Such pipeline failures can cause devastating environmental and capital damage.
Automated orbital pipe welding with TIG applies to pipelines in the oil and gas industry. The process provides exceptional precision, weld quality, and above all, consistency. These factors improve productivity and weld inspection pass rates. The oil and gas industry often uses cladded pipes and exotic, custom-formulated alloys. Both need stringent adherence to weld procedures, and orbital welders can meet these demands. Orbital welding heads for pipeline welding, like the AMI Model 15, are both rugged and precise. Even in adverse outdoor conditions. So, while the process is technical, we can use it in demanding environments with the right equipment.
Pharmaceutical And Biotechnology
Advances in the medical field, and exceptional medical professionals worldwide, have led to huge gains in recent times. Eradicating some of the most debilitating diseases, like polio. The fight against cancer and other health maladies continues. But year on year, R&D engineers, scientists, and medical professionals are making inroads. Improving the successful treatments for the worst health problems every year. So pharmaceuticals and medical devices are manufactured in facilities with the highest standards.
The large-scale production of fluids, tablets, capsules, and vaccines includes hazardous chemicals. Processing, storing, and distributing, of these products is safety critical. Working personnel welfare is also a huge priority every step of the way. A weld cannot be responsible for a contaminated batch because lives could be at risk. This is why sterile tube welding in the pharma industry is one of the most regulated jobs on the planet.
These high-purity industries have the most demanding requirements for pipe and tube cleanliness. Which includes standards for high-purity fusion pipe welding. This is especially important for CIP (Clean in Place) and sterile WFI (Water For Injection) systems. Sanitary tube and pipe welding in these industries rely on the orbital TIG process to meet stringent codes and standards. Orbital welding is the most reliable method to produce accurate and smooth welds without crevices. As well as reducing loss of corrosion resistance, or contamination of the product. Orbital TIG welding helps to save lives by allowing us to create complex, functional, and safe medicine production systems. Welding these systems by hand would be almost impossible!
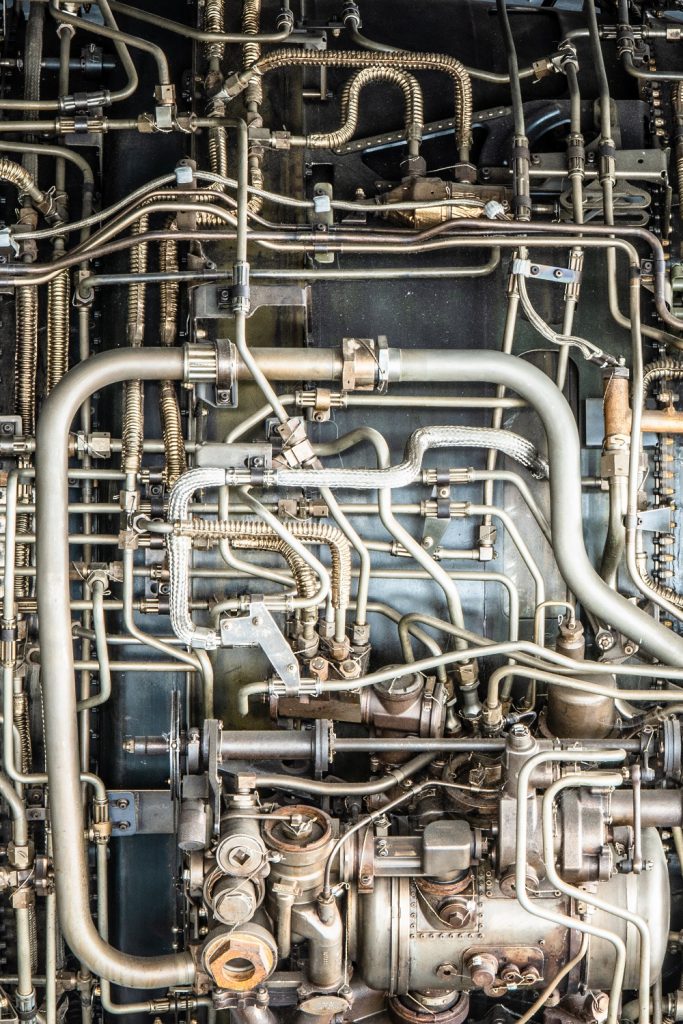
Aerospace Orbital Welding Applications.
Have you ever heard the saying that flying is safer than driving a car? It’s true. Research by Harvard University shows that flying in the US, Europe, and Australia has a 1 in 1.2 million chance of a flight accident. While the chance of a fatal car crash is 1 in 5000! Today, flying is safer than ever, and according to MIT, flight safety increases year after year. Of course, this is thanks to the brilliant engineers. Innovating and improving the airplane navigation, engine, and flight systems. But, orbital welding plays a significant part in turning engineering ingenuity into reality.
Airplanes can have thousands of critical fuel and hydraulic control lines. This is the main orbital welding application in the aerospace industry. These are exposed to complex cyclical loads and thermal stresses. Joining these tubes requires absolute process control, because any mishap can lead to a compromised joint. If this burst, it would present a major safety hazard. The welded joint must not negatively impact the alloy’s characteristics. Or contribute to corrosion, develop cracks, and not distort. The heat input control is paramount, and computer-controlled orbital welders are up to the task. The aerospace industry was the first to introduce orbital welding, and still relies on its near-perfect characteristics. Creating powerful, safe, and awe-striking airplanes. Including the likes of Boeings and Airbuses.
Power Generation
Fossil fuel and nuclear power plants rely on orbital welding to meet stringent requirements. A single weld failure at a critical point could pose a significant safety hazard. Creating a high capital loss in these facilities. But to make matters worse, the tubes in power generation plants are often tightly packed. Meaning limited space for construction and welding.
Orbital welding systems are the industry’s standard for boiler tube welding (tube to tube). As well as constructing heat exchangers. Other orbital welding applications in this sector include economisers, superheaters, reheaters, and tube lines. Thanks to their weld head’s compact size, versatility and accuracy. As well as adaptability and exceptional weld quality, orbital GTAW provides excellent joint integrity. Meeting the demanding needs of power generation.
Orbital Welding Applications in Shipbuilding
Large cruise and naval ships can be hundreds of meters long and tens of meters high! For example, the largest UK Navy aircraft carrier is the HMS Queen Elizabeth Class. It stands at 280 meters long and 73 meters high! Likewise, cargo ships or vessels that transport crude oil can be of enormous dimensions. Such ships can take years to produce, with substantial time devoted to welding the hull plates and piping systems.
Modern ships have many piping systems, including engine cooling, steam, and fire protection. As well as bilge, water, and fuel systems. These piping systems are challenging to weld because of stringent quality requirements. The constricted spaces also offer their own challenges. The welder’s safety can often get jeopardised due to welding in cramped areas. Where the welding fumes can quickly displace the breathable air. Plus, these piping systems must be accessible for weld repairs while at sea. Emergency contingencies can need prompt welding repairs to save people on board. But quality construction prevents such events from happening in the first place.
Orbital welding can join small and large diameter tubes and pipes in cramped areas. Completing the task with near-perfect weld quality. The shipbuilding industry uses orbital GTAW to pass safety and welding quality codes and regulations. Some vessels can have their own nuclear power generators! This complicates the construction and amplifies safety hazards. These ships can require welding titanium, high nickel, and many specialised alloys. Orbital TIG welding easily achieves exceptional welds on these materials.
Westermans – Meet Your Orbital Welding Needs
Are you looking to buy, rent, or sell your orbital power sources and weld heads? If so, we’re here for you! Contact ustoday, and our experts will help you choose the best orbital welding equipment for you. Premium brands like AMI, Magnatech, Orbitalum, Fronius and ESAB, are available from stock today! View them here.
comments
Pingback: All You Need to Know! - Autotruckpartsoutlet.com
Pingback: All You Need to Know! – Mynewcaraccessories.com
Pingback: All You Need to Know! – Tracktodirt.com