TIG welding, also known as Gas Tungsten Arc Welding (GTAW), is a highly versatile and efficient welding process. It’s proven to be ideal for pipe applications, with its precise control and ability to produce high-quality welds. TIG pipe welding offers several more advantages over other welding techniques.
In this article, we will take a closer look at the benefits of TIG welding for pipe applications. Including why it is the preferred choice for many professionals in the industry. From its ability to create clean, precise welds, to its suitability for a wide range of materials. TIG pipe welding offers unmatched performance and reliability. Whether you are working with stainless steel, aluminium, or other alloys, TIG welding ensures superior strength and durability. Join us as we delve into the advantages of TIG welding for pipe applications. Discover why it continues to be the go-to method for achieving flawless welds in various industries.
Understanding TIG Pipe Welding Applications.
Pipes play a crucial role in various industries, including oil and gas, construction, and manufacturing. They transport fluids, gases, and other materials, making them an integral part of many systems. The welding process used in pipe applications is of utmost importance. It determines the strength, durability, and integrity of the pipes. TIG welding has become the preferred method for joining pipes in these industries. This is due to it’s precise control and ability to create clean, high-quality welds.
TIG welding involves the use of a tungsten electrode and a shielding gas to protect the weld pool from contamination. The tungsten electrode, which does not melt during the process, provides heat to the base metal. While the shielding gas prevents oxidation and ensures a clean weld. This combination of heat control and shielding makes TIG welding an ideal choice for pipe applications. When the integrity of the welds is paramount.
TIG welding also offers the advantage of being a manual or automated process. This allows welders to have complete control over the welding parameters depending on the application. This level of control is especially important in pipe applications, where precision is crucial to ensure leak-free joints and optimal performance. With TIG pipe welding, welders can adjust the heat input, welding speed, and electrode position. Helping to achieve the desired results, resulting in strong and reliable welds.
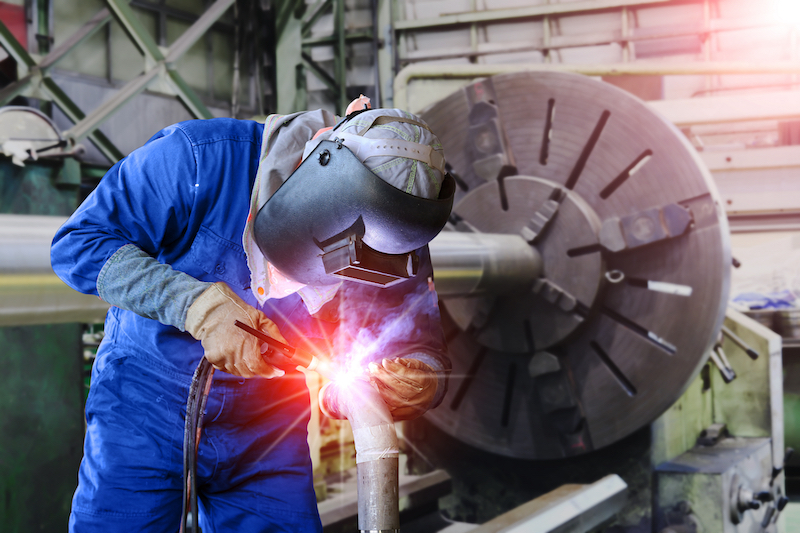
The Advantages of TIG Welding for Pipe Applications
Increased Precision and Control when TIG Pipe Welding.
One of the main advantages of TIG pipe welding is increased precision and control. The nature of TIG welding allows welders to have complete control over the welding process. Ensuring accurate and consistent results. This is particularly important when working with pipes that need precise alignment and fit.
With TIG welding, welders can adjust the heat input and welding parameters to match the requirements of the application. This level of control allows for the creation of clean, precise welds that meet the highest quality standards. Whether it’s a small-diameter pipe or a large-diameter pipeline, TIG pipe welding ensures that the joints are strong and leak-free. Making them able to withstand the demands of the application.
Superior Weld Quality and Aesthetics.
TIG welding is renowned for producing high-quality welds with excellent aesthetics. The precise control, coupled with the use of a tungsten electrode and a shielding gas, results in clean and visually appealing welds. This is important in pipe applications where the appearance of the welds can be a significant factor. As well as their visual appeal, TIG welds also offer superior strength and durability.
The process allows for thorough fusion of the base metals. This creates a strong bond able to withstand the stresses and pressures experienced in pipe applications. This ensures that the welded joints remain intact. While also preventing leaks and ensuring the long-term performance of the pipes.
Minimised Heat Distortion and Warping.
Heat distortion and warping are common challenges in welding, particularly in pipe applications. The heat generated during the welding process can cause the base metal to expand and contract. This leads to defects like distortion and warping, resulting in misaligned joints and compromised structural integrity. All contribute to increased repair and maintenance costs.
TIG welding helps cut heat distortion and warping due to its low heat input and precise control. The focused heat provided by the tungsten allows for localised heating, reducing the heat affected zone. Reducing distortion and warping, ensuring that the pipes maintain their shape and alignment.
Versatility for Various Pipe Materials and Thicknesses.
Another significant advantage of TIG welding for pipe applications is its versatility. The TIG process is suitable for various materials and thicknesses. These include stainless steel, aluminium, and carbon steel, as well as exotic alloys. This makes it suitable for diverse pipe applications across different industries.
Furthermore, TIG welding can handle both thin and thick pipe walls with ease. The precise control allows welders to adjust parameters like heat input and welding speed, to match the thickness of the pipes. This versatility ensures that TIG welding can be used for a wide range of pipe applications. From thin-walled pipes used in HVAC systems, to thick-walled pipes used in oil and gas pipelines.
TIG Pipe Welding: Critical Applications
In critical pipe applications where safety and reliability are of utmost importance, TIG welding shines. Industries such as nuclear power, aerospace, and pharmaceuticals are great examples. Needing welds that meet stringent quality and safety standards. TIG welding is the preferred choice for these high-stakes applications. Due to it’s ability to produce clean, defect-free welds.
The regulated heat input and precise control of TIG pipe welding ensures that welds meet the required specifications. Whilst enabling them to withstand the extreme conditions and pressures they’re exposed to. Whether it’s a nuclear reactor pipe or a pharmaceutical processing pipeline. TIG welding provides the reliability and performance necessary for critical applications.
TIG Pipe Welding Techniques
While TIG welding offers several advantages for pipe applications, it is essential to understand and use the proper welding techniques to achieve optimal results. Certain considerations and techniques must be taken into account when TIG welding pipe. This will optimise the integrity and strength of the welds.
One crucial technique is the proper preparation of the pipe joints before welding. Like ensuring clean, smooth surfaces free, from contaminants that can compromise the weld quality. Proper fit-up and alignment of the pipe joints are also critical. Making sure that welds are strong and leak-free.
Another important technique for TIG welding pipe applications is the use of proper welding parameters. Things like selecting the appropriate welding current and electrode size. As well as shielding gas flow rate based on the pipe material and thickness. Welders must also maintain a consistent travel speed and control. While the tungsten electrode’s angle and position to achieve optimal results. This is where automation and orbital welding can be very beneficial.
Safety Considerations for TIG Welding in Pipe Applications
Safety should always be a top priority when performing TIG welding in pipe applications. Welders must take necessary precautions to protect themselves and others from potential hazards. This includes wearing personal protective equipment (PPE) like welding helmets, gloves, and clothing.
Proper ventilation is also crucial in all situations. Welders should ensure that the workspace is well ventilated to prevent the accumulation of harmful fumes and gases. Additionally, proper grounding and electrical safety measures should be followed. This will prevent potential electrical accidents.
TIG Pipe Welding: Conclusion
TIG welding offers a multitude of advantages for pipe welding applications. Helping to make it the preferred choice for professionals in various industries. From increased precision and control, to superior weld quality and aesthetics. TIG welding ensures strong, durable, and aesthetic welds. It’s ability to cut heat distortion and warping, as well as it’s versatility for various pipe materials and thicknesses are also benefits. Further solidifying it’s position as the go-to method for achieving flawless welds.
Whether you’re working in critical pipe applications or everyday pipe installations. TIG welding pipe provides the performance, reliability, and safety required for successful welds. By understanding the proper techniques and considering safety measures, welders can harness the full potential of TIG welding. Achieving optimal results in their pipe welding applications. Experience the unmatched quality and durability TIG welding pipe offers for your needs.
comments
Pingback: The Advantages of TIG Welding for Pipe Applications – Motorbrute.com
TIG welding is indeed a highly versatile and efficient process, particularly for pipe applications. The precise control and ability to produce high-quality welds make it an excellent choice. I appreciate how this article highlights the advantages of TIG welding, such as increased precision and control, superior weld quality, and minimized heat distortion. These factors are crucial for achieving accurate alignment and maintaining the structural integrity of pipes.
It’s also great to see that Westermans offers a wide range of used industrial welding and fabrication equipment. This provides a valuable resource for those in need of reliable machinery.
Overall, this informative article showcases the benefits of TIG welding for pipe applications, and Westermans’ expertise and offerings in the welding industry. Keep up the great work! Rick Tillman
Thanks for your comments Rick, it’s a slower, more involved process but the results speak for themselves for critical applications!
Pingback: The Advantages of TIG Welding for Pipe Applications - Autotruckpartsoutlet.com
Pingback: The Advantages of TIG Welding for Pipe Applications – Mynewcaraccessories.com
Pingback: The Advantages of TIG Welding for Pipe Applications – Tracktodirt.com