Plasma cutting consumables are components in your plasma cutter. They wear over time, and need to be replaced.
Optimum Cutting Performance:
Consumables have a life-cycle.
The consumables are all found in the cutting torch itself, which is where most of the energy is focussed. Keeping track of wear and tear is a key part of maintaining an efficient machine. Ensuring it cuts well, and lasts a long time.
Plasma cutting torch consumables include: a swirl ring, electrode, nozzle, retaining cap, and shield cap.
Types of Plasma Cutting Consumables.
Swirl ring.
This is a small component inside the torch that swirls the gas surrounding the plasma arc. This outer layer of gas helps to focus and direct the arc for greater cutting precision. Whilst swirling it helps to keep it cool. This protective layer of gas surrounding the arc makes contact with the nozzle. Lowering temperatures and preventing the nozzle from burning up and slowing down degradation.
Electrode
The electrode is a narrow piece of copper containing hafnium; an excellent conductor of electricity. It’s job is to receive the electrical current from a connected cathode block inside the torch. Focussing the charge through its tip, which causes it to arc onto the workpiece.
Nozzle
The nozzle focuses the plasma arc and the gas that surrounds it, making a clean and precise cut.
A nozzle with a larger opening is used for gouging. While a nozzle with a smaller opening is better at directing the gas for fine, detailed work.
Retaining Cap
The retaining cap essentially holds all of the consumable parts of the torch together. As temperatures are so high, it’s not just the parts in contact with the arc that are worn down. The component holding them together also degrades over time due to the extreme conditions.
Shield Cap
The shield protects the torch and its components from the sparks and molten metal resulting from the plasma cutting process. It takes the brunt of the fallout, minimising wear to other components as much as possible.
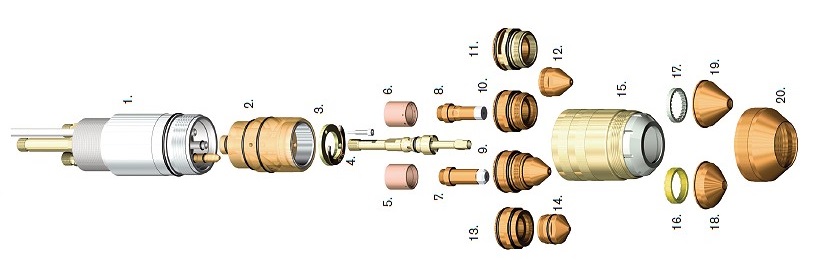
How long do plasma cutter consumables last?
Now that we’ve looked at the role each of these consumable parts play, we’ll move on to discuss how long these elements last.
The nozzle and electrode wear out more quickly than other components. This is because they are creating and focussing the cutting arc.
You’ll notice nozzle wear primarily in the quality of the cut you are achieving.
As the nozzle wears, the hole in the tip gets larger, making the plasma arc thicker. Thus producing a wider cut (kerf) in your workpiece.
You will be able to see with a visual inspection when the nozzle hole is too large and needs replacing.
When to Replace Nozzles and Electrodes.
As the electrode produces the arc, the hafnium insert melts and over time fragments are shot out through the torch in the cutting process, resulting in the development of a pit in the end of the electrode. This is perfectly normal, but when the pit grows deeper than around 1-1.6 mm you’ll need to replace the electrode, as there won’t be much hafnium left, and you’ll soon start burning through the electrode itself. This will make it extremely difficult to cut and could significantly damage the rest of your torch components.
Variables to Consider.
It’s hard to be specific about exactly when you should be replacing your nozzle and electrode.
It will depend on factors including; the speed you cut, material thickness, and the amperage you use. However, it is a good idea to replace your nozzle and electrode at the same time (according to whichever wears out first). Doing this gives you optimum cutting performance, rather than using a new electrode with a worn and inconsistent nozzle, for example.
When to Replace Other Components.
Your other components won’t need replacing so often. Being mainly vulnerable to dropping, slag from the cutting process, thermal dynamics and heating and cooling cycles.
Check your swirl ring and retaining cap for cracks, and replace as soon as any appear.
It’s good practice to be changing your swirl ring every fifth electrode replacement if you can.
Cleaning the shield cap of slag ensures consistent airflow, replacing it when the build up is too large to remove.
Replacing your consumables at the right time is essential for the maintenance of your machine and the accuracy of your cut. And you can rest assured that here at Westermans International, our partnership with Hypertherm means we can supply you with genuine plasma consumables of the highest quality.
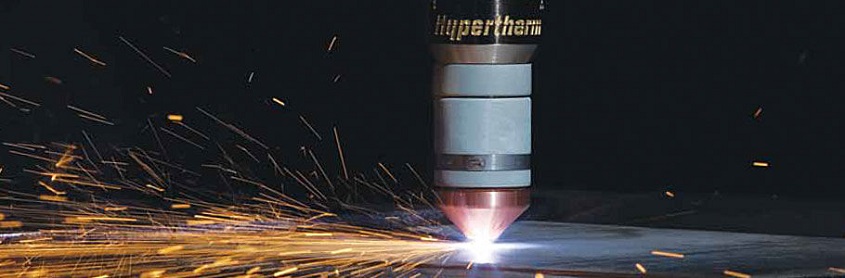
3 TIPS TO PROLONG THE LIFE OF PLASMA CUTTER CONSUMABLES
- Cutting parameters: Cutting too quickly, too slowly or at the wrong distance from your workpiece will wear your parts more quickly.
- Correct installation: Installing your components carefully and correctly is essential if they are to function properly. This includes making sure the tolerances of the consumables match the amperage you’ll be using, as well as correct assembly.
- Monitoring: Keeping track of how your components are wearing will enable to you prevent one worn component prematurely degrading others. You’ll need to change your nozzle and electrode more frequently than your other parts, and leaving them too long will put added strain on the whole system, as well as reduce your cut quality.
Need more advice on Plasma Cutting?
Read our Blog on the Top 4 plasma cutter gases
For more tips and tricks visit Hypertherm’s own website for lots of helpful advice to get the most out of your plasma cutter.
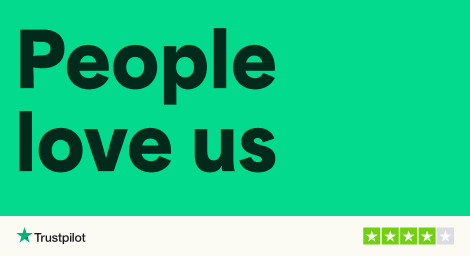