Welding work brings hazards. A systematic approach to safety to avoid them requires training, expertise, skill and mindfulness from employers and workers.
Electrical, ergonomic, mechanical and work environment hazards are among the other dangers welders may encounter.
I think we all recognise that not everybody can just go and weld. You’ve got to be trained. You’ve got to be competent and capable. You need to know exactly what you’re doing.
Here are some of the major hazards workers may encounter when welding and how to protect against them.
Confined Space Working
Confined space working is the lack of oxygen. You may be working in an identified confined space, but you should also be aware if your work space could become a confined space as you weld. Inert gases and some common chemical reactions (for example rusting) can reduce the amount of oxygen inside enclosed spaces such as tanks, pipes and pits. Working in these locations is dangerous. Plan before you enter a confined space:
Consider if there is a way to do the job without going in if you have to go in, use a safe system of work. Make sure you know what the emergency rescue plan is. Never use oxygen supplies to ‘sweeten’ the air (this is a very serious fire risk) Welding gases such as argon, carbon dioxide, nitrogen and helium can displace the air inside enclosed spaces. Argon and carbon dioxide are relatively ‘heavy’ gases. They can pool in places where you do not normally expect to have a problem, for example vehicle inspection pits.
Sometimes inert gases are used to deliberately replace the air to prevent weld oxidation or reduce the risk of fires. Gases may also build up as they are used during the welding process. If you don’t follow the safe system of work and enter an area where there is a large amount of inert gas, you are risking death from asphyxiation.
Confined spaces:
Read more…… A brief guide to working safely gives more guidance on this.
Preventing Fires and Explosions
Where hot work cannot be carried out in a safe area, or where combustible material cannot be removed from the work area, a fire watch should be maintained during and after the hot work.
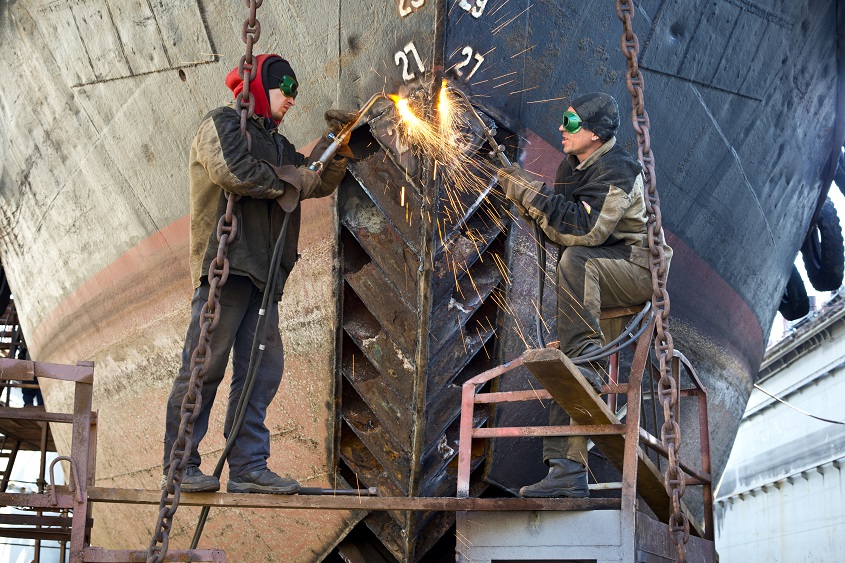
This watch should be maintained for at least 30 minutes after the completion of the hot work, but where an unintended ignition may be difficult to detect or slow to develop, this may need to be extended to 60 minutes.
Welding and cutting inside ships and other enclosed spaces is particularly dangerous as smoke from fires cannot escape and will quickly overcome people working nearby.
Explosive atmospheres can be caused by flammable gases, mists or vapours or by combustible dusts. If there is enough of a substance, mixed with air, then all it needs is a source of ignition to cause an explosion.
Each year people are injured at work by flammable substances accidentally catching fire or exploding. Work which involves using or creating chemicals, vapours, liquids, gases, solids or dusts that can readily burn or explode is hazardous. The effects of an explosion or a fire in the workplace can be devastating in terms of lives lost, injuries, significant damage to property and the environment, and to the business community.
Most fires are preventable, dealing with workplace process fire safety is important and those responsible for workplaces and other non domestic premises to which the public have access can avoid them by taking responsibility for and adopting fire safe behaviours and procedures.
Electrical Hazards
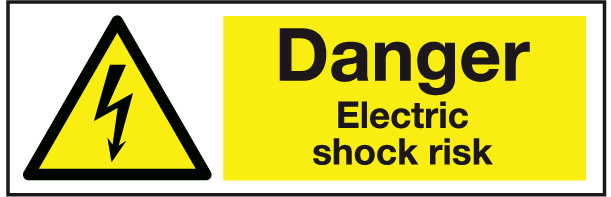
The arc welding process requires a live electrical circuit. This means all arc welders using hand-held equipment are at risk of electric shock and electrical burns. The risk for MIG/ MAG and TIG welding is much less, as the welding current is normally switched on and off using the trigger or foot switch. One culprit is damaged welding leads, When this happens, the electrical circuit is no longer contained. Arc welding uses an electrode cable that powers the welding lead and a ground cable to create that circuit. Damaged or improperly maintained equipment – such as cables or missing/burned out insulators, or faulty connections – can cause shock injuries or electrocution. Another danger: Some welders attempt to replace a welding electrode or contact tip with their bare hands, instead of wearing a dry welding glove. Don’t become complacent and forget the basics. It’s hot and you are sweating and you’ve changed wire or contact tips hundreds of times without gloves, but now you are wet and things could happen.
Burn Hazards
Welding exposes workers to intense heat – often thousands of degrees – making burn injuries common. Wearing the proper personal protective equipment, along with inspecting and maintaining it, is a key step to preventing burns. This can mean making sure gloves and clothing don’t have holes; using flame-resistant hearing protection; and not wearing clothes with cuffs or open pockets, where sparks or molten metal can become trapped.
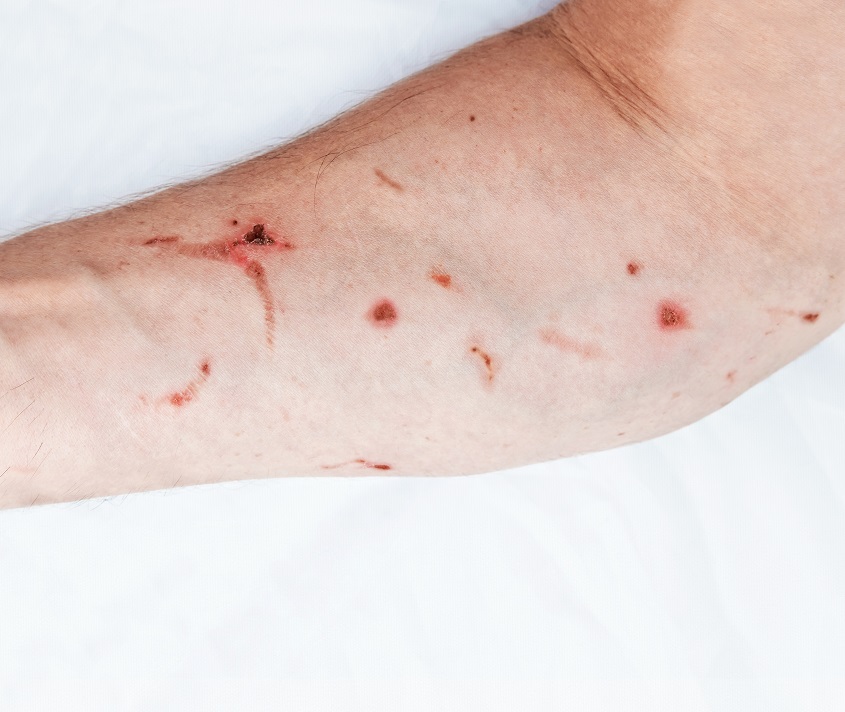
Radiation Hazards
Another source of burns is radiation, or electromagnetic energy, that reaches the skin. One form of radiation, ultraviolet rays, can be harmful to workers’ eyes – resulting in “welders’ eye” or “arc eye” (a reference to arc welding). Sometimes the effects are not felt until several hours after an exposure, warns the Occupational Health and Safety organisations.
Symptoms may include mild pressure to intense pain in the eyes, bloodshot eyes, eye irritation (a feeling like sand in the eye, according to CCOHS) and sensitivity to light. Employers must ensure welders wear helmets with the proper shade of filter plate.
Welding Fume Hazards
Recent laws and regulations regarding Fumes mean that lower exposure limits are a must for the workforce who are subjected to smoke and fumes from welding and metal cutting.
International health organisations recognise the importance of preventing health risks associated with fumes and smoke generated during welding and thermal cutting. In many countries, strict personal exposure regulations and standards such as are heavily enforced to minimise worker exposure to hazardous metal particulate that can be present in welding fumes.
Ventilation and filtration are the primary solutions to mitigate employee exposure. Welding fumes are generated by a thermal process that creates a plume of suspended particles in the ambient air. When the fume plume cools, the particles enter the breathing zone affecting worker exposure. Properly designed capture and filtration systems protect worker´s health and assist in complying with local regulations and standards.
You can either use a mobile or fixed fume extraction unit where the ducting arm acts as an exhaust to clean the air. Or you can have your own PPE known as PAPR (powered air purification respirator unit) like in the image below.
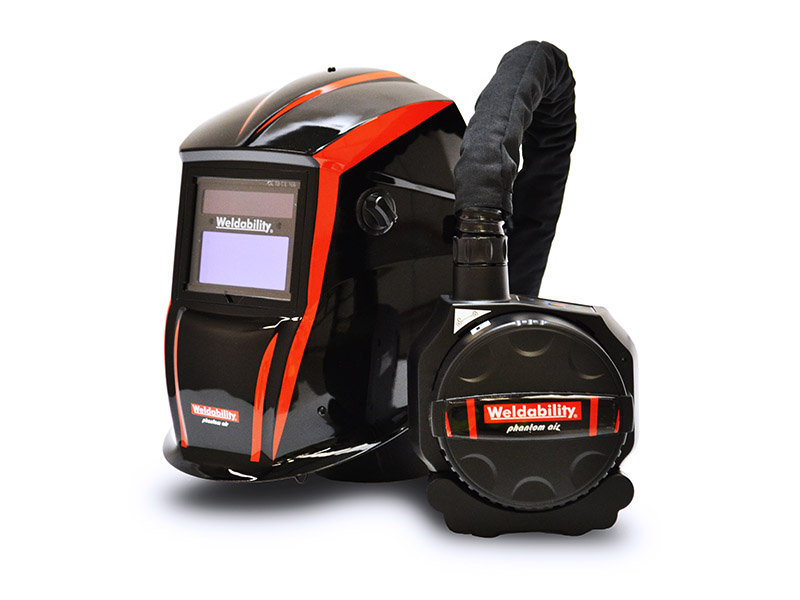
AWS provides additional tips, including wearing a welding helmet and safety glasses with UV protective side shields. The organisation also advises the use of a screen, curtains or adequate distance to avoid exposing other workers to radiation, and having anyone near the welding or cutting area wear safety glasses with UV protective side shields. You can learn lots here on the organisations Health and Safety section
As a welding equipment and accessory supplier we are here to help you provide a safe environment for you and your co-workers. Click here for protection products or give us a call to see how we can help reduce hazards in the workplace.