Is this something you are guilty of? We take a look at the calibration process and why you could be risking your hard earned reputation by not renewing certificates.
Calibration is a measurement process that assigns values to the property of an artifact, or response of an instrument, relative to reference standards or to a designated measurement process.
The purpose of calibration is to eliminate or reduce bias in the user’s measurement system, relative to the reference base.
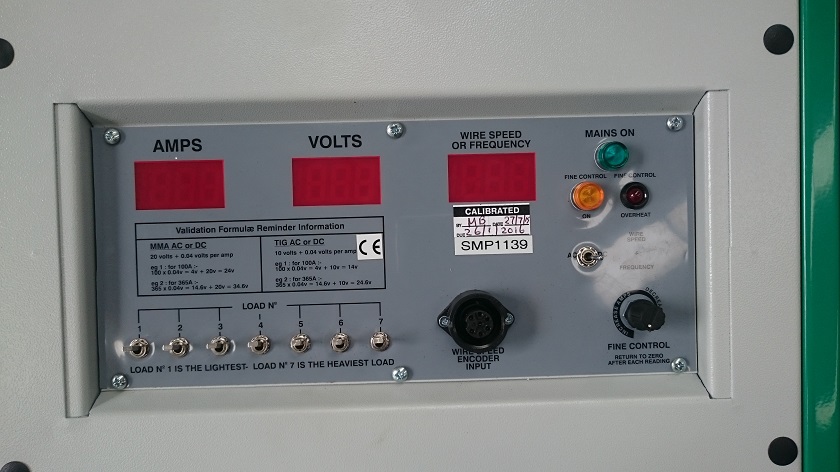
If you are working for a company with high levels of welding technology, it is essential that systems deliver consistent welding results without failing throughout their service life.
What is calibrating?
The process of calibrating welding systems involves them being connected up to a calibration station to have their voltage, amperage, and wire feed speed measured.
It is also an option to determine the gas flow rate of the welding current source.
The calibration software analyses the values recorded for your welding systems, then compares them against the standard specifications in order to identify the discrepancy between the two.
This result must fall within the permissible tolerances as set out by the European (EN) 50504 standard.
If a company does not take these required steps, they should not continue to use the welding machine for production. This is based on considerations surrounding quality assurance and product liability.
Investing in a welding calibration unit and/or a load bank unit will save you more than money.
Benefits and Requirements
As a general rule, MIG/MAG, manual metal arc welding, and TIG systems can be calibrated. If you are a certified fabricator, you are required to calibrate your welding equipment on a regular basis.
The standards set out the principles for the quality assurance process for welded products.
EN 1090 defines the production standards and CE markings for steel and aluminum supporting structures.
Read more about ISO 9000 series and EN ISO 3834-2.
If you comply with the standards, you will find yourself in a position to gain your customers’ trust and to build up a reputation as a professional enterprise.
Not to mention that being able to prove calibration has been performed can come in handy in the event of complaints.
There’s no denying that regular system maintenance comes at a cost in the short term. However, it’s nothing compared to the long term price you will pay if you cannot prove that your production process is in line with the standards, in the event of damage occurring.
Accidents cause harm to people as well as steel constructions.
As you know, it is your company’s responsibility toward your customers to guarantee product quality. You can achieve this by regularly calibrating welding machines and equipment, ensuring it is best practise.
Top Tip
Combine safety inspections with calibration as an effective way of saving time and money.
A portable calibration unit is the ultimate tool for validation of welding equipment. Add a Load Bank to the package and you will have all the data you need to comply to safety regulations.
If you are looking to carryout in-house calibration of your welding machinery we can supply several types of calibration machines. We can provide training here at our site or at your own premises.
Please contact us to discuss which would be the most suitable unit to buy.
Author: Claire Spillane – Director of Westermans International, Buyers and Sellers of Used welding and cutting equipment – Mum and Nana
comments
We need more advice. Our customers are in need.
What sort of advice would you like?
Simple to use units – plug into your machine and see what is its optimum performance.
The blog you published here is very nice and informative. As you can see, calibration is of the utmost importance for welding machines. When it comes to welding, proper calibration, gear, and air tool repair services are a must-have. So before you get started on a new project, get your welding system calibrated first.
Cheers Tom, great to get your take on calibration.